Mechanical Ventilation in a building is an essential part of creating comfortable conditions for the occupants. There is an entire science involved: too much air can lead to higher energy bills, too little and we can create dampness and unhealthy zones!
Ventilation also has an impact on our primary fire safety strategy, compartmentation. The use of ducts can create potential consequences in a fire that can inhibit safe evacuation and make fires more difficult to contain and control.
There are 5 scenarios we need to consider
Of special attention are areas where fire ductwork is used and it crosses a protected route or lobby. The element of the duct crossing these areas must have the integrity from EN13501-3 and also insulation. This is to offer protection to those using these areas in the event of a fire.
Historically, we didn’t give much attention to the need for insulation properties. However, as our understanding of fire risk has developed, insulation is seen as critical in preventing secondary fires during an incident. The standards and particularly the classification reports EN13501-4 and EN13501-3 have defined the system as being critical. The combination of ducts and insulation in tests, have revealed the importance of both elements contributing to providing the EI S classifications (E = Integrity, I = Insulation, S = leakage).
Thor Duct® has been tested extensively with uninsulated and insulated solutions. This ensures a safe solution for every fire scenario. As our industry evolves, we will continue to channel this knowledge to our clients, and test and prove the full suite of Thor Duct® products to ensure our clients are getting the safest, most compliant solutions available.
Need To Know More?
Contact us today to find more about training and CPD from Thor Duct®.
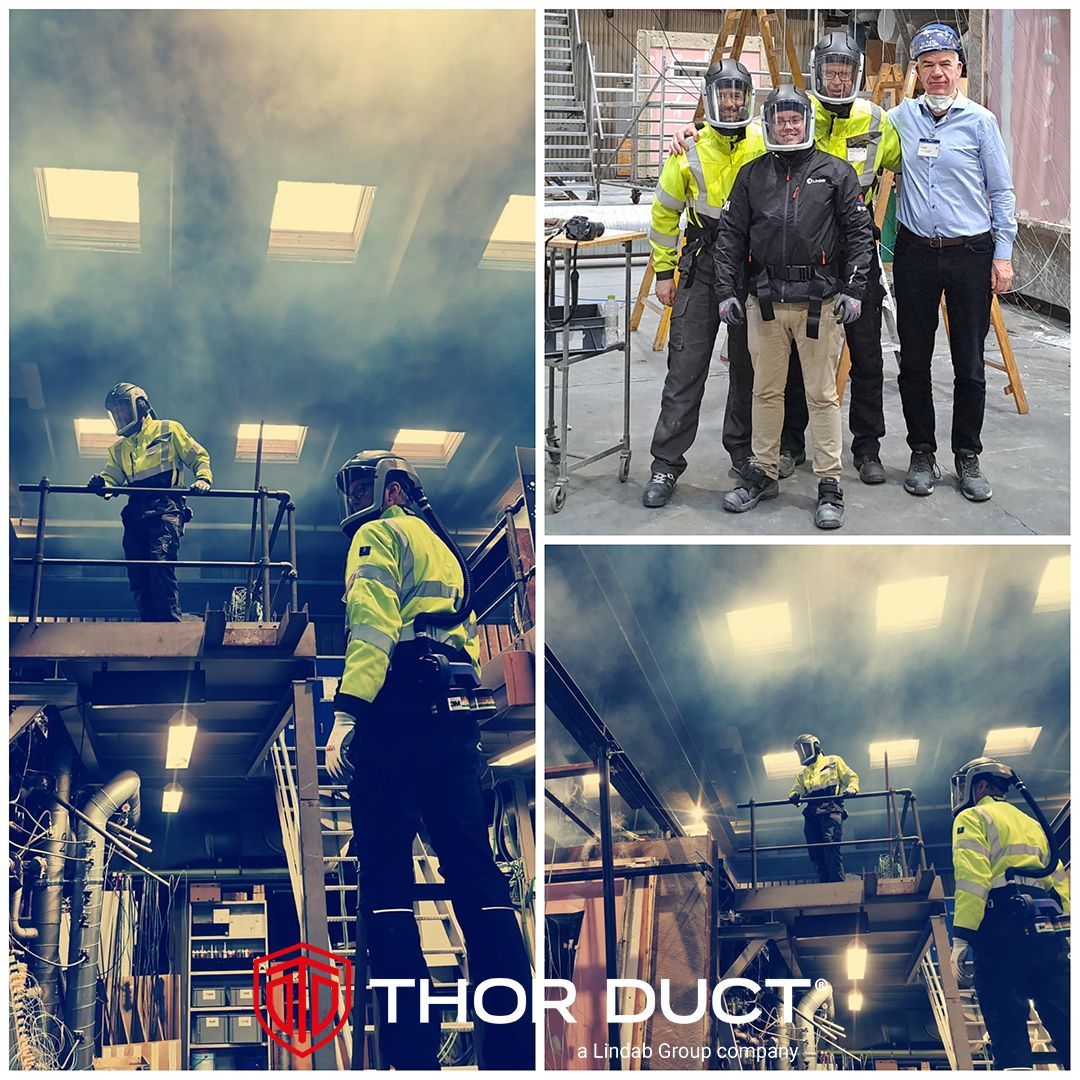
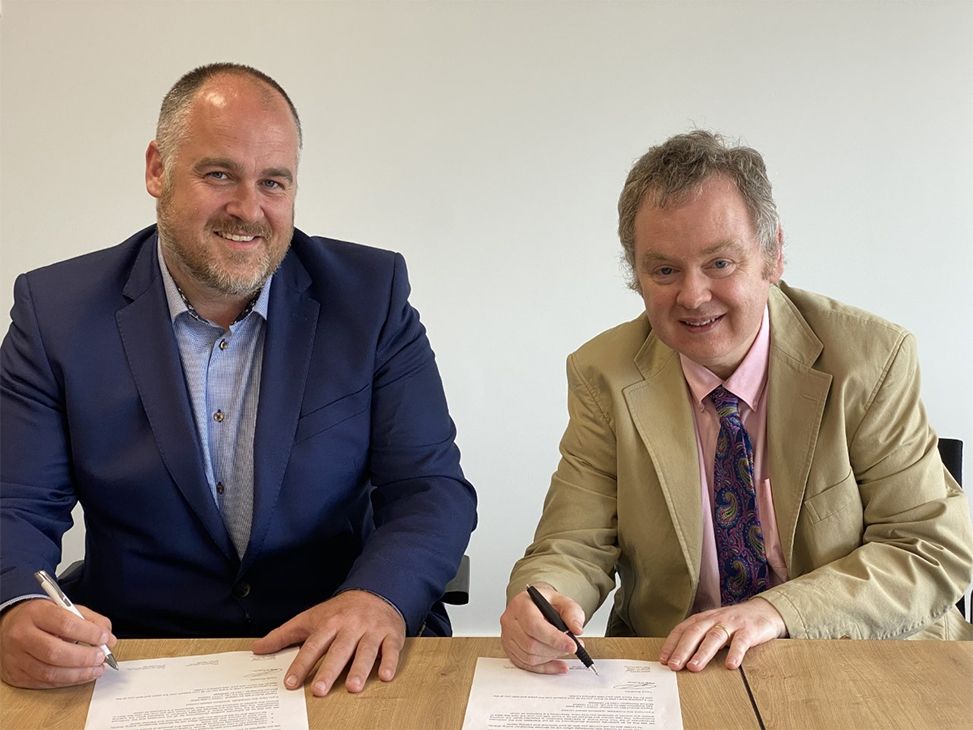
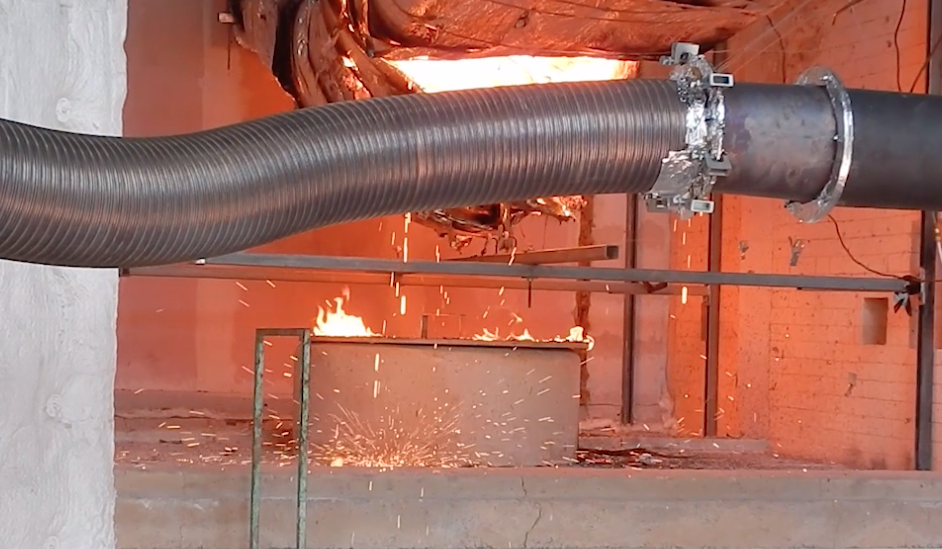